物流業界では今、「人手不足」「作業の属人化」「事故の多発」など、
深刻な課題を解決する手段として、AIやロボット、自動化システムの導入が急速に進んでいます。
・AIによる作業量予測
・AGV(無人搬送車)による自動走行
・自動ピッキングロボット
・データベースによる在庫管理の最適化
・トラック予約・受付システム
これらの技術を導入すれば、
「現場は変わる」「事故は減る」「人はラクになる」――はずでした。
しかし実際には、現場で“うまくいっていない”例が後を絶ちません。
■ なぜ、うまくいかないのか?
現場のリアルには、AIにもロボットにも読み取れない“人間ならでは”の動きがあります。
たとえば…
・AGVのルート上に台車が置かれて止まってしまう
・ピッキングロボットが“空き箱”をつかんで動けなくなる
・荷役現場に貼られたバーコードが汚れて読めなくなる
・自動化エリアにルール表示がないため、作業員が間違って立ち入り
・映像で研修したが、現場に出ると“忘れていた”と言われる
どれも、人の行動・習慣・思い込み・不満・気の緩みといった
“アナログな感覚”を設計に織り込めていないからこそ、起きている問題です。
■ 「人を動かせない」技術は、現場では使えない
物流現場では、“人が動く”ことが前提です。
どんなにAIが進化しても、ロボットが導入されても、人が関わる限り、事故のリスクはゼロにはなりません。
だからこそ、最初に必要なのは「この現場で人がどう動くのか?」を考える“アナログ視点”なのです。
■ アナログで“現場が動ける仕組み”を先に整える
・誰が見ても「ここに立ち入ってはいけない」とわかる表示
・AGVルート上に「台車を置かない」と伝えるピクトと誘導線
・バーコード位置を作業の邪魔にならないよう視覚誘導する表示
・点検中に触ってはいけない場所を、色と形で強調する注意表示
・初めてのドライバーでも迷わず駐車できる大きなサイン表示
こうした“アナログの工夫”があるから、デジタル機器は安全に機能できるのです。
■ 現場で機能するのは、「わかる化サイン」+「現場の関与」
そこで注目されているのが、
「現場が自ら考え、必要な表示をすぐ作って貼れる」仕組みです。
それを実現するのが、DAPS(デジアナプリントシステム)です。
・現場スタッフが「この表示が必要」と声をあげ
・デザインをパソコンで考え、プリントし
・実際に貼ってみて、効果や反応を確認し
・必要なら改善して再出力
まさに「人を動かすために、現場が考える」プロセスそのものです。
■ デジタルの前に、アナログで“人の動き”を整える
技術だけでは現場は変わりません。
「どう使われるか」まで含めて設計するアナログ的な視点こそが、
DXや自動化を機能させる“土台”になります。
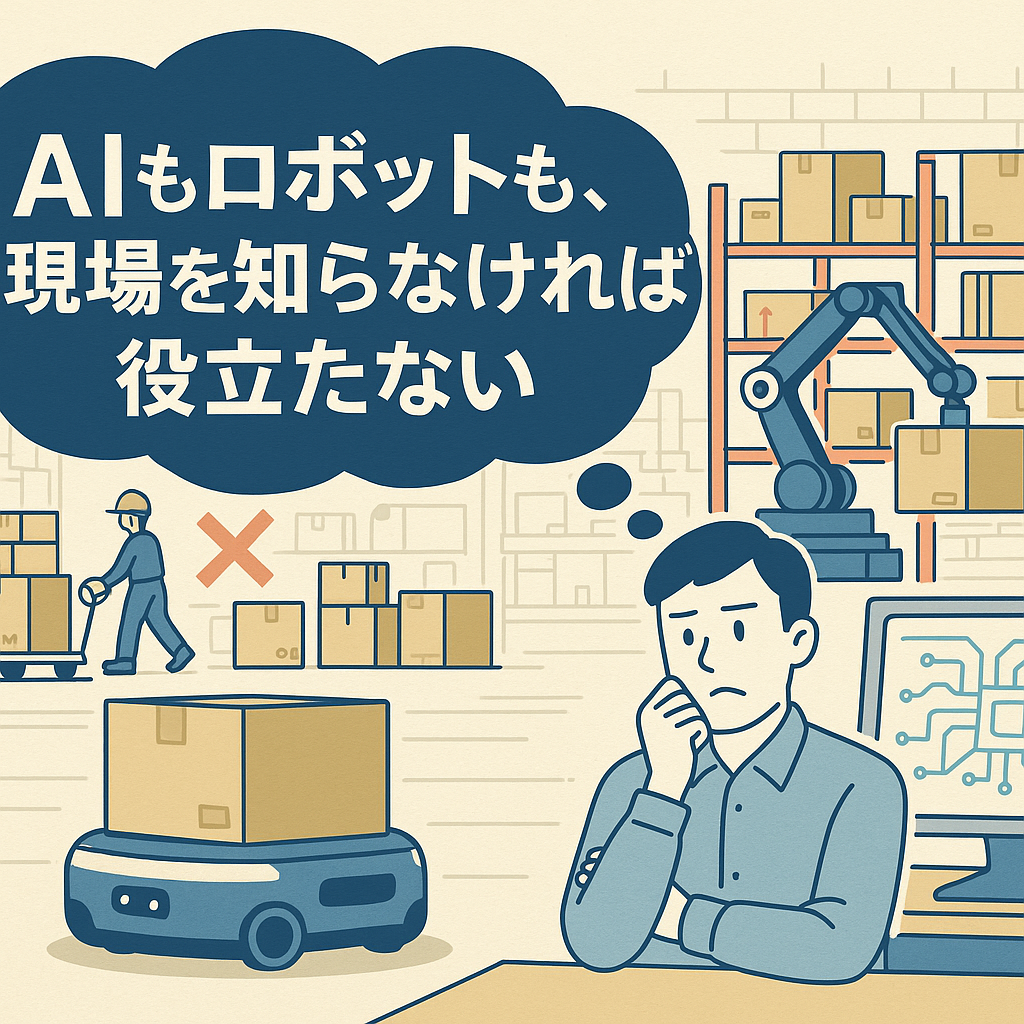